Material Escalation – Big actors in late 2021
- Christopher DeBruyn
- Sep 16, 2021
- 2 min read
Updated: Jul 25, 2023

I hear lots of talk in the marketplace about escalation, anecdotes about troubled buy-outs, supply delays and general chaos. Anecdotes about one client driving up steel for the entire country are far-fetched, but several market segments are experiencing demand outside of the general market trend.
In a May 2021 blog post I discussed higher prices for mill steel, and softwood lumber that were all over the news. Nearly 6 months later, things are looking clearer, if not much better. Lumber has peaked and is resuming a more normal pricing level, while steel products continue to rise, lead by a tripling of cold formed products like deck and joists. Hot rolled steel shapes have shown a more modest increase, but are still also on the rise.
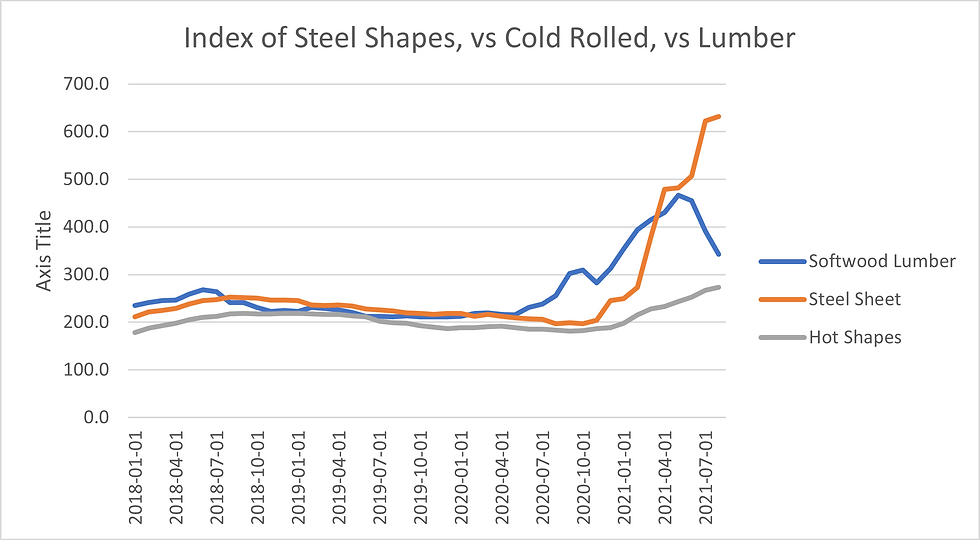
ENR adds a piece to the picture in a recent poll of construction firms that show 89% of trade contractors have problems finding skilled craft workers. Firms are also reporting project delays due to extended lead times, shortages of materials, and delivery delays.
So material costs are rising, based on economic data from the Fed shown in the graph above. Labor rates are up, and availability of labor and materials is challenging construction trade firms.
Ed Zarenski, in his Construction analytics blog projects notes that total spending in commercial non-residential construction is down 10% from January 2020, and should continue to rise as the project backlog of stopped and stalled projects from early 2020 continues to move forward to their peak employment periods, and new projects are started and continue.
However the remarkable material cost increases, and labor shortages are happening in spite of the slowed non-residential construction, which is not forecast to recover until 2023.
Looking forward, as I said in May:
1) Supply disruptions. Lead times continue to be extended for many products, so close management of supply schedules will be critical to minimizing schedule slippage. Contractors are encountering difficulties in procuring materials at times, which will either result in declining margins (and probably performance), change requests for unforeseen costs, and slipping schedules.
2) For the near term, expect material cost shocks for steel (structures, siding, piping, equipment, etc.).
3) Price spikes for various manufactured items as the production facilities and transportation modes adjust to rapidly changing market demand.
References:
Steel/Lumber Index – Federal Reserve Bank of St. Louis
Labor and Materials Escalation – ENR Building Cost index
Construction Analytics – Ed Zarenski
Comments